Звезды гиганты и сверхгиганты02.07.2018
Звезды карлики01.07.2018
Биосфера земли28.06.2018
Солнечная радиация22.06.2018
Крупнейшие вулканы30.03.2018
Отбор керна13.09.2017
Нефтесервисные компании11.09.2017
Призабойная зона09.09.2017
Бурение буровыми растворами17.08.2017
Висбрекинг - процесс, сырьё, установка03.08.2017
Трудноизвлекаемая нефть23.07.2017
Повышение нефтеотдачи21.07.2017
Бурение горизонтальных скважин19.07.2017
Наклонно-направленные скважины16.07.2017
Попутный нефтяной газ07.07.2017
Бурение высокооборотным турбобуром
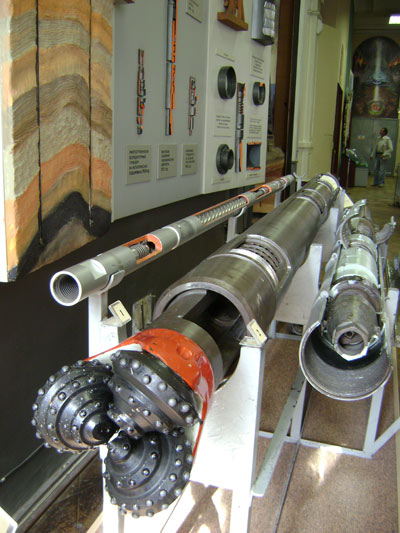
Турбобур – вариант бурового устройства, состоящего из электрогидравлического движка, принцип действия работы которого, основан на превращении энергии движения буровой смеси в энергию движения вала. Назначение такого агрегата – разработка скважинных отверстий для добычи газовых и нефтяных месторождений.
Как все начиналось?
Задаток такого агрегата начал появляться в 20-х годах прошлого века. 1922 год – ознаменовался в СССР изобретением первого турбобура. В этом изобретении одноступенчатая турбина на высоких оборотах сообщает движение долоту посредством редукторного механизма, который наполнен масляным составом.
1938 год – использование безредукторного турбобурного устройства, полезной мощностью 100кВт уже с большим количеством ступеней. В этом экземпляре вал непосредственно сообщает движение долото.
Отличительной чертой такого бура является то, что такая установка является открытым типом, в ней вал крутится в подшипниках на основе резины и металла, которые охлаждаются за счет циркуляции промывочной жидкости. Момент вала считается суммированием моментов, которые дает каждая ступень.
Начало 50-х годов знаменательно тем, что разработчики стали искать пути решения проблемы по увеличению количества ступеней турбины. Это необходимо было сделать, чтобы снизить частоту вращательных движений долото. Тогда были разработаны первые агрегаты, состоящие из двух и трех секций. Они собирались уже непосредственно на территории проводимых работ. Секции приходилось свинчивать по резьбе в виде конуса, а валы присоединялись муфтами: сначала использовались конусные, а затем конусно-шлицевые муфты. Нижняя часть секции была оснащена стержневой опорой агрегата.
Через некоторое время разработчикам удалось переконструировать установку и как результат – эксплуатационные моменты агрегатов стали проще, и стержневая опора стала автономной деталью – секцией и преобразована в шпиндель. Такое новшество способствовало замене на месте самой истершейся части установки – опоры.
50-е годы - их окончание - были ознаменованы тем, что разработчикам пришлось думать над тем, как повысить эффективность бурения, поскольку резинометаллическое основание значительно понижало производительность турбобура, если использовались утяжеленные смеси, или в них попадало много шлака. Поэтому в итоге проектировщики подошли к проектированию опоры качения, которая должна была сгладить все погрешности.
На начало следующего десятилетия пришлось создание упорно - радиальной шаровой опоры. Она включала в себя подшипник качения с массой уровней.
Затем созданный агрегат продолжал свое развитие. Появилось новшество: шарошечные коронки с опорами, заполненными масляным раствором и полностью герметизированные. Эти коронки при 100% результате требовали частоту вращательного движения от 2,5 до 5 с. Такой факт сподвигнул разработчиков к дальнейшему проектированию новшеств для усовершенствований конструкций агрегатов бурения.
Появлялись все необычные витки развития конструкций:
- появилась система гидродинамики;
- многосекционные;
- появился клапан-регулятор смеси;
- смягчение вибраций;
- движение жидкости стало разделяться, и появился пустотелый вал;
- статор стал приходить в движение;
- появилась тормозная приставка, основанная на гидромеханике;
- разрабатывалась приставка редуктора;
- разрабатывались винтовые двигатели, основанные на гидравлике.
Типы турбобуров
- секционные стандартизованные шпиндельные агрегаты – складываются из четырех составляющих - секций: три из них турбинные, а четвертая шпиндельная. Во всех турбинных составляющих имеется: по 100 уровней, по 4 радиальной опоры и по 3 уровня предохранительной пяты.
- агрегаты с высоким моментом и с конструкцией гидроторможения – состоят из 3 секций и шпинделя. Вращательное движение ротора дает обратную силу турбине агрегата.
- агрегаты, состоящие из большого числа секций – вал агрегата оснащен турбинными составляющими - сборками. Здесь расположено не менее 3 секций;
- агрегат с независимой подвеской – все секции турбины снабжены упорным шарикоподшипником. Коническая резьба объединяет корпусы секций, а полумуфты в виде квадрата объединяют валы. Все секции вмещают от 80 до 90 уровней;
- агрегат с движущимся статором – опора шпинделя в оси несет усиленный вес. Все статоры такой конструкции беспрепятственно движутся вдоль оси;
- агрегат с пустотелым валом – у агрегата имеются шпиндель и секции турбин;
- агрегат с изымаемым редуктором – отличается тем, что эта составляющая всегда может быть подменена на месте.
Бурение высокооборотным турбобуром
Данный метод бурения предусматривает отправку на площадку отбитой горной массы агрегата с коронкой. Смесь подается в агрегат с константой по расходу. Также создается и изменяется вес на забой. Поскольку агрегат может развить реактивную мощность, которую определяет частота вращательных движений, при бурении нужно учитывать то, что скачки давления должны быть постоянны. Это можно выполнить с помощью регулировки забойного веса и корректирования и сохранения значения давления на отметке близкой к максимальной, в трубопроводе циркуляционной системы.
Устройство такого типа оборудовано:
- агрегатом с коронкой, установленном на колонне;
- инструментом передвижения в отверстии бурения;
- системой движения смеси;
- интерфейсом фиксирования давления смеси, связанным посредством информации с панелью пуска инструмента бурения.
Данный пульт, запрограммирован на определенную потребляемость смеси, и поддержании уровня давления близкой к максимальной.
Составляющие турбины агрегата – статор и ротор – имеют необычную конструкцию лопаток. Кромки лопаток выполнены со специальной угловой составляющей, а углы лопаток ротора и статора отличаются.
Бурение таким способом не совсем удобно, поскольку сопротивление породы к вращательному движению инструментов, уменьшает максимальный крутящий момент. Он определяется расчетным значением тормозного момента и у него отсутствует зависимость по глубине бурения, движению долота, стержневого веса на коронку и нет зависимости от того, какие породы приходится проходить, то есть, зависимости от их свойств нет.
Данный метод способствует увеличению прочности труб приблизительно в десять раз в параллели с роторным бурением. Это доказано практикой. В данном типе бурения большое значение играет передача мощности от энергоисточника к коронке: он получается больше в отличие от роторного бурения.
Минусовые факты
Минусами всех методов работы турбобуром является то, что максимум скорости, который выдает составляющая проходки, не обуславливает максимум скоростного движения долото за маршрут, отсюда можно сделать вывод о том, что агрегат не работает на уровне максимальных затрат, то есть его невозможно вывести на режим максимума по выдаваемому результату. И на это не способен ни один бурильщик, или автомат.
Минусами всех устройств, которые содержат пульты выдачи бурильного агрегата, является как раз несостоятельность аппаратуры контролирования значения максимального значения в работе агрегата.
Все турбины также имеют недостатки, которые выявляются в том, что поверхностное бурение не обусловлено максимумом мощности агрегата, процесс работы буром нельзя принять в оценке: максимально ли значение мощности на определенном промежутке или нет. Поддержание такого режима так же невозможно.
К тому же, у турбин момент относится так низко к частоте вращательного движения, что увеличение глубины долота за оборот имеет малое значение, а это снижает движение и саму проходку долота за маршрут. У турбин плохой запуск агрегата. Помимо этого, в разгоняемом режиме срабатываемые напоры завышены, что предупреждает аксиальную опору, когда агрегат доводится до забоя отверстия.
Характеристики турбобура
У агрегата должны иметься следующие характеристики:
- так как обособленный расход жидкости равен 0,07л/с на 1 см2 забойной площади, то агрегат должен иметь нужный момент кручения;
- агрегат должен безопасно работать на пониженной частоте вращательного движения (меньше 7с – шарошечные коронки и меньше 10с - алмазные коронки);
- коэффициент полезного действия должен быть максимальным или приближен к максимальному значению;
- должны быть обеспечены скачки давления не меньше 7МПа на коронке;
- больше 300 часов – таким должен быть задел на отказ;
- больше 2000 часов – такой должна быть жизнеспособность;
- характеристика энергии должна являться константой и не меньше, чем задел на отказ;
- энергетическая составляющая не должна обуславливаться показателями давления и температуры окружающей среды;
- микрореологические свойства смеси, должны поддаваться изменениям при долблении;
- допустимость корректировки свойств смеси путем добавления разнообразных примесей;
- допустимость выполнения очистки бурильного отверстия от устья до забоя, в отсутствие движения коронки;
- допустимость выполнения измерений - линии движения ствола, во всех местах без поднятия устройства выполнения работ;
- выходной вал при первой необходимости должен входить в стопор, и также свободно выходить из него;
- вибрация бурильных агрегатов должна гаситься;
- затраты проходки на 1 м должны быть экономичны, чем в альтернативных методах бурения.
Конструкция должна содержать все эти требования, поскольку они способствуют экономичности и целесообразности бурения. Однако на деле все это непросто.
Однако в наши времена на практике часто встречаются низкооборотные средства бурения, такие как роторные (редукторные низкооборотные турбобуры и винтовые забойные двигатели).
Преимущества перед другими методами проведения работ
Плюсы использования данного агрегата вместо винтовых забойных двигателей:
- КПД значительно выше по потреблению энергии;
- процесс выполнения работ возможен даже при высоких температурах на забое;
- получаемый ствол более прямой (отсутствие изгибов и перекосов);
- при снижении давления на забое, возможно, использовать аэрированные смеси;
- понижение в несколько раз вибрации, которая ускоряет износ инструментов бурения и понижает эффективность их работы;
- у винтовых забойных двигателей наблюдаются также продольные вибрации ротора относительно статора – это из-за угла откоса в блоке управления (регуляторе). Наблюдается потеря энергии при трении скольжения. Это приводит к большому нагреву резины на статоре и как результат – ее износ;
- вращение роторного узла выдает большую кинетическую энергию и как результат – момент кручения более - плавный;
- небольшой реактивный момент;
- более защищен от засорения;
- допустимость использования при врезании, в более проницаемые впитывающие пласты, крупно-разделенных смесей;
- период эксплуатации между ремонтными работами значительно больше и превышен в 2 - 4 раза;
- управление в процессе бурения улучшено, как при наклонном, так и при боковом;
- метр проходки стоит намного меньше – это происходит из-за продолжительной работы на забое и уменьшения СПО.
Сюжеты по теме
Нефть дешевеет на опасениях эпидемии коронавируса22.01.2020 10:47
Сейсмологи прогнозируют крупное извержение вулкана Тааль21.01.2020 13:09
Нефть снова дорожает20.01.2020 11:26
Украина не будет строить газопровод для СПГ из США17.01.2020 10:29
Белоруссия ищет альтернативу российской нефти16.01.2020 10:46
Вулкан Тааль на Филиппинах выбросил двухкилометровый столб пепла15.01.2020 10:31
Разгадана загадка Солнечной системы о «великом водоразделе»14.01.2020 10:54
На Филиппинах началось извержение вулкана Тааль13.01.2020 10:44
Газпром резко сократил подачу газа в Европу10.01.2020 12:02
8 января был официально открыт «Турецкий поток»09.01.2020 10:45